CNC plasma cutting machine is also known as CNC Plasma cutter. Just as the CNC wood router and CNC laser cutting machine, the CNC Plasma cutter are also widely used for industrial cutting process. Before that, we must know what exactly does this plasma means. So, let’s dig in.
What is Plasma?
Plasma is the fourth state of the matter besides solid-state, liquid-state, and the gas-state. By heating water, we can change its state to gas. If we further burn gas, it will turn into the ionized form. Finally, we call it a plasma.
What is a CNC Plasma cutting machine?
CNC plasma cutter is an automated cutting machine. CNC means computer Numeric Control. Any name along with CNC is an example of the automation technology. However, after the 19th century, we got the advancement of the various CNC machines.
Consequently, A CNC Plasma cutter is an automated plasma cutter machine which has a plasma cutting tool can cut the electrically conductive metals. So, we can find that the main difference between the CNC cutting machines is in their cutting tool.
The structure of Plasma cutting machine
The basic structure of the plasma cutter has three main components. They are,
- Power supply: A plasma power supply converts the AC power supply to the smooth DC power supply. Usually, the range of the DC power supply is between 200 VDC to 400 VDC. This DC power supply maintains the whole process from the plasma arc throughout the cut. Based on the material types and thickness, it also regulates the current output required.
- Arc Starting Console: The ASC or Arc Starting console has the critical task to do here. This ASC produces the Alternating current 5000 VAC. It provides the spark inside the plasma torch. And then, it creates the plasma arc.
- Plasma torch: This part is the foundation of the overall cutting process. It maintains the alignment of the cutting process. It also provides the cooling system. The main components required for the arc generation is the electrode, swirl ring, and the nozzle. We can add a new cap to get a better cutting quality.
Plasma Cutting Principle
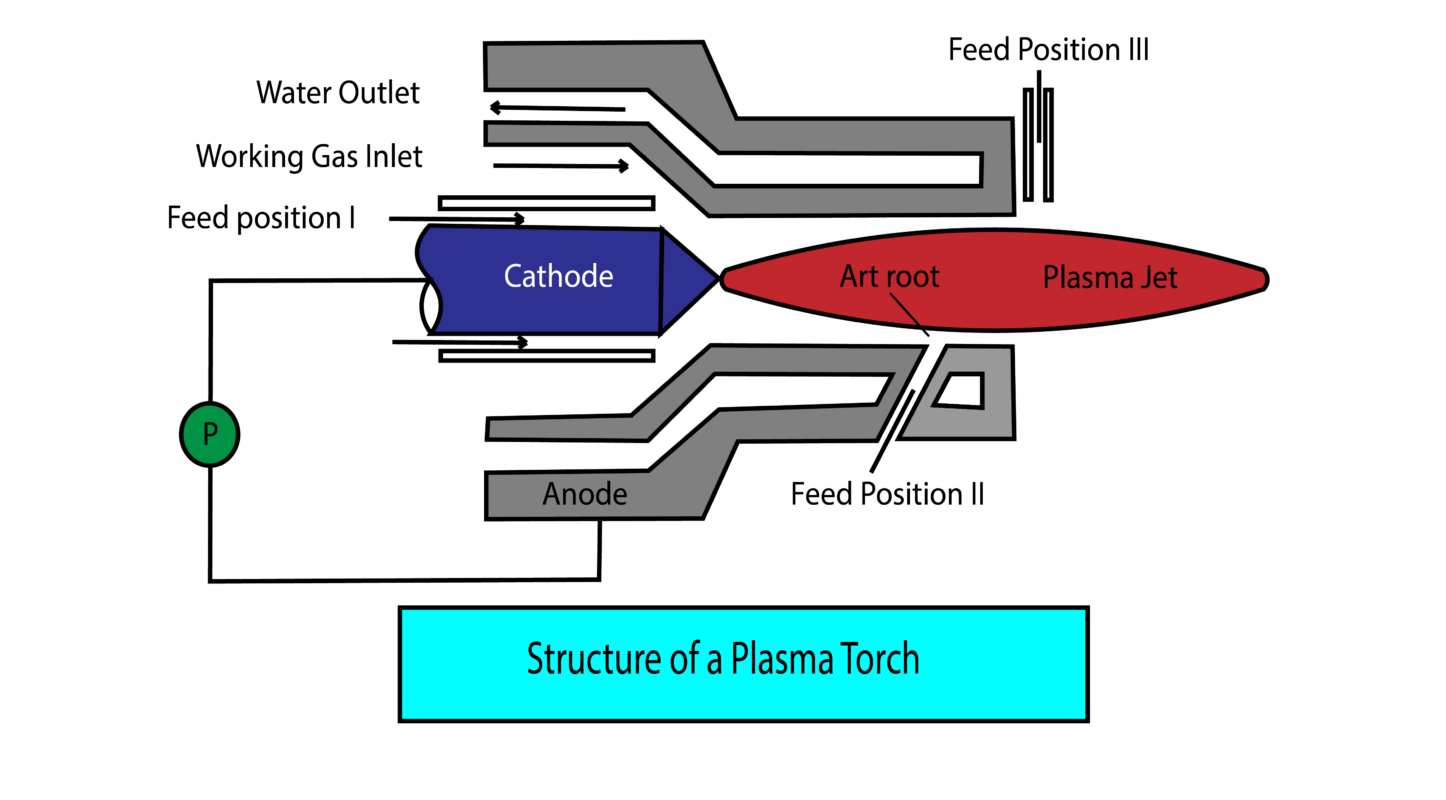
First, we need a gas particle to start the process. The gas can be many types such as oxygen, nitrogen, argon, or even shop air. But often, most of the plasma torch in the workshop uses the shop air. There’s a pressurizing device that forces this gas to get inside the plasma torch.
And then, this high pressured gas flow meets an electrical arc generated. It turns into the 40,000˚ F. We can call it as a plasma jet. Subsequently, we will find the negative cathode that makes the plasma jet into the negative plasma.
At this time, we know the object we are dealing with is the electrically conductive material. Therefore, this negative plasma jet can quickly melt down positive metal. Finally, we have performed a cutting.
We should note that a plasma cutting can only perform for the electrically conductive materials. We will describe more about it in the elements for the plasma cutting section.
CNC Plasma cutting principle
Similar to the other CNC machine, CNC plasma machine also performs the same working principles. First, the operator must save the design of the cutting on his/her computer. Using CAD software, we can keep the configuration in CAD format. And then, We can use the required CNC software to convert our design into the machine processing language.
However, through the particular cable, the instructions passed to the machine. Now, its time to work on the object. The working table has three primary moving rail system. On the three of the climbing rail, there are three stepper motors.
The design we gave in the machine has converted the CAD design into the pulse function of the stepper motor. The pulse function is the time of the motor rotation. Therefore, depending on the number of the pulse, the stepper motors push the cutting tool on the desired cutting line.
Finally, the plasma torch throws the negative plasma jet on the electrically conductive materials. It quickly melts down.
Targeted materials for plasma cutting process
As we have mentioned above, a plasma torch can cut only the electrically conductive materials. The materials are such as steel, stainless steel, aluminium, copper, brass, and some other conductive materials. We should note that we can not cut plastic, wood, or other non-metallic electrically non-conductive materials using the plasma torch.
Applications of CNC Plasma Cutting machine
CNC laser cutting Vs. CNC plasma cutting. Which one is better? Both of them cut metals, then why the application of them is different? These are the common question we get from our customers. Well, there’s a difference between them.
- CNC laser cutter can cut the operation, which needs a lower tolerance range. On the other hand, the CNC plasma cutter cuts the bevel cutting.
- The more complex design needs a CNC laser cutter. But the CNC plasma cutter performs the simple cutting operation.
These two are the fundamental difference between their working principles. Let’s have a glance at the application of the CNC plasma cutter.
- In the robot welding work station, the CNC plasma cutter performs different operations.
- In Marine welding and cutting, the uses of CNC plasma machine is more than the other fields.
- CNC plasma machine also works at the auxiliary welding machine
- In the steel structure pipeline manufacturing, CNC plasma cutter has a remarkable position.
Types of CNC Plasma Cutter
There is some renowned brand for plasma cutting in the recent market. For example, Hypertherm plasma cutter, Lincoln plasma cutter, Thermal dynamics plasma cutter, Esab plasma cutter. Based on the position of the anode and the cathode, the CNC plasma cutter has two classes in common. They are,
- Traditional Plasma cutter: This type of plasma cutter throws a negative plasma. It has the cathode electrode in the middle of the torch and the surrounding as the negative.
- Inverter Plasma cutter: This type of plasma cutter is just opposite of the traditional plasma cutter. It has a positive electrode in the middle of the plasma torch. The surrounding body works as a negative electrode.
Based on the plasma jet
Based on the number of gases used in the plasma jet, we can further classify them into five types.
- Conventional Plasma Cutter: This type of plasma cutting usually uses a single gas generally air or nitrogen. A traditional plasma of CNC cutter is suitable for 5/8″ thick of the materials. So, The cutting is usually ideal for handheld operation. Most of the plasma torch has a rated current of 100 Amps.
- Dual Gas Plasma Cutter: This type of Plasma cutter generally uses two gases. One of the gas is for the plasma jet and the other one for the shield. The shield gas is necessary to cover the cutting area. It provides the best possible cutting.
- Water Shield Plasma Cutter: This process is quite similar to the dual gas plasma cutting. But instead of the second gas, this type uses the water to shield the cutting area. It produces improved nozzle workpiece cooling. It also provides better cutting.
- Water Injection Plasma Cutter: This type of plasma cutter uses a single gas for the plasma jet. It utilizes water directly injected into the arc. The amps required for this process is usually from 260 amps to 750 amps. This process is for high-quality cutting of several materials. The cutting thickness can be more than conventional CNC plasma cutting.
- Precision Plasma Cutter: This type of Plasma cutter performs superior cutting quality on thinner sheet metals. The size less than 1/2″ of thick. This process usually is slower than the other methods.
plasma cutting machine types Based on the dimensional cutting
Based on the dimensional cutting, the plasma cutter further has two types. They are,
- Two axis CNC plasma cutters can cut in two directions. Though there are three stepper motors for moving in 3D. But while cutting, the plasma torch can cut only X and Y-axis. And this is a two-dimensional plasma cutter.
- Three axis CNC plasma cutters can make 3D sculpture. Technically, the plasma torch can rotate and move based on the requirements. And thus, this type is a 3D CNC plasma cutter. For example, 3D Automatic CNC Pipe Tube Plasma Flame Cutter Beveler is from Shandong Kasrey Intelligent Equipment, etc.
The Basic Structure of the CNC Plasma Cutter
The following are the essential parts that we must discuss.
- CNC operator: There is a leading operating machine that commands the primary mechanical mechanism is the CNC operator. We can input the program manually on this device. Or we can convert our CAD design into the CNC language and transfer that to this device.
- Plasma Table: The working table on which the plasma torch performs its activities is a plasma table.
- Guide rail: There are 3 x 2 guide rails on the plasma table. The different axes move on this guide rail. The position of the tracks depends on the structure of the CNC plasma cutter.
- Motors: There are three stepper motors are available. Based on the size of the working table, motor power depends. The heavier the weight is, the more powerful the stepper motor is.
- Working stage: We know that the plasma is super hot ionized. So after cutting, it must cool down. So, to shield this thing, the CNC plasma cutter uses water or other gases to cool it down. Therefore, there is an evacuating system on the working stage. Several screws help to tighten the object.
- Sensors: There are multiple sensors situated on the working bench. It helps to locate the plasma torch.
How to choose a CNC Plasma Cutter?
As we have said above, that the CNC laser cutting and CNC plasma cutting has a similar cutting principle. But there are only two differences between them. So, Before we go for choosing a CNC plasma cutter, we must know on which purpose we need a cutting machine.
While you decided that you must need a CNC plasma cutter, then we recommend considering the following essential points.
- Duty Cycle is the period that calculates the number of cutting the plasma cutter can perform in every ten minutes before it needs to cool down.
- Output power is the ability to cut the object. For example, a 12 amps output power of 120V machine can penetrate 1/8″. On the other hand, 60 amps output power of 230 V can penetrate 7/8″ of the sheet metal.
- We must have to choose conductive materials to cut. Plasma cutting is not suitable for non-metals.
- The speed of plasma cutting is vital to consider. The general rates of the plasma cutting are inch per minute (IPM).
- Plasma torch: We have seen there are five kinds of the plasma torch. Therefore, depending on our demands, we must choose the right plasma torch for cutting.
Advantages
- It cuts with wide cutting areas almost all conductive sheet metals.
- It has a fast cutting speed and higher efficiency.
- Cutting accuracy is higher than flame cutting. The cutting underwater is not deformed.
Disadvantages
- It can not cut non-metals.
- The cutting thickness is shallow, the higher the depth is, the higher power it needs.
- Plasma cutting is bevel shaped.
Precaution
- We should allow any unauthorized personnel inside the lab.
- There should be a distance between the observation and the cutting area.
- We must ensure the fire extinguisher before the operation.
- While handling the gases and fumes, we must be careful.
- We must ensure our safety.
Maintenance
- After working, we must clean up everything.
- We must ensure that our machine is powered off.
- After cleaning up, we should put back every tools and equipment we took before the operation.
Summary
After all, we hope we have covered all of the possible pieces of knowledge that we must learn. In this short article, we have tried to demonstrate the introduction to a CNC plasma cutter. However, if you are a beginner in this field, we strongly recommend mastering the precaution and safety manual first.
However, we hope we could make an easy learning way for you. If you are interested in other CNC machine technology, we have demonstrated a summary of them in the link attached to the CNC machine technology.