One of the most widely used technologies is LASER (Light Amplification by Stimulated Emission of Radiation). Laser devices typically amplify a light beam to produce a small but powerful focal point. Various industrial laser applications have emerged as a result of this principle. As a result, one of the most often discussed subjects in laser technology today is laser marking vs laser engraving.
Today’s topic will clarify the confusion between laser marking vs laser engraving. Furthermore, this article will demonstrate the various types of laser machines with distinct laser source principles.
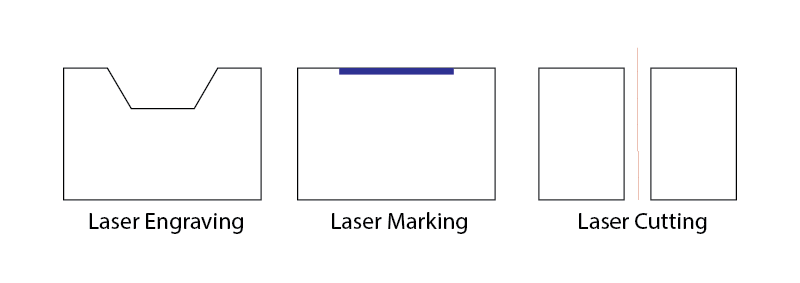
What is Laser Engraving?
In laser engraving, typically the laser beam separates surface material from the projected area. As a result, various surface textures are formed. For example, harsh elements look black during metal laser engraving, whereas smooth structures seem white.
The usage of laser metal engraving is frequent in everyday products. For Example, If you have awards and trophies from your school or college, you may be curious about the name engraved on the surface of the trophy. Other standard laser engraving uses barcode authentication, decorative products, medical and electronic equipment, signs, etc.
Working principle of the laser engraving process
In the laser metal engraving process, the engraved surface is created using a combination of melt and evaporation ablation processes. The laser beam is so powerful that it melts and partially evaporates the material during processing.
The laser engraving creates a depression in the material. An engraving depth of 10 to 50 meters, for example, is normal. The vapor pressure of the evaporating substance pushes the melt outwards, forming a melt rim as it cools.
Because it is challenging to drive away from the melt ultimately, the engraving is U-shaped and grows narrower as the laser cuts further into the material. Due to the narrow laser spot and shortish temporal pulses, the heat input is confined locally.
Laser engraving has different processes depending on the mark’s types. The following are the procedures most often used for laser engraving.
Blackening
When engraving metals using the laser beam, the melted primary material interacts with air oxygen, generating oxides that vary in color. Because rough surfaces absorb a lot of light, the marking is generally black or dark gray for aluminum or dark brown for steel, brass, and copper, based on the type of materials.
Whitening
Whitening minimally structures the surface to melt the substances. In materials like galvanized steel, it generates a clean, reflecting surface as a white marking. The coating remains intact and corrosion-resistant due to the minimal penetration depth.
However, on dark metals like hardened steel, high-contrast whitening is extremely useful. A black and white engraving mix is incredibly suitable for applying data matrix codes. It enhances code quality and legibility by increasing contrast.
What is Laser Marking?
In its most basic form, laser marking is an irreversible process that employs a focused light beam to leave a permanent mark on a surface. Laser marking covers many applications and is often familiar with fiber, pulsed, continuous wave, green, or UV laser equipment.
These machines are capable of marking most metals and non-metals at high rates and with permanent traceability markings. The laser marking machine has a wide range of uses, but it is most commonly used to mark logos, words, brands, dates, series numbers, batch numbers, signs, drawings, pictures, QR codes, etc.
In electrical devices, including integrated circuits, mobile communications, precise instruments, glass watches and clocks, and computer keyboards, you may also find it.
Working principle of the laser marking process
Laser marking works by marking the surface of a substance with a focussed beam of light. When the beam interacts with the material’s surface, it changes its characteristics and appearance. This focused beam exclusively targets a specific region, allowing the laser marking machine to generate accurate, high-quality, high-contrast marks on nearly any surface.
Because of this property, laser marking is appropriate for situations where precision and permanence are vital to success. Recently, two broad ideas have become increasingly widespread in laser marking technology.
Hot-working
The hot-working process usually also employs a higher energy density of the laser beam and irradiates on the surface of the processing material. The material surface absorbs the laser energy, causing a thermal excitation process in the irradiation area. As a result, the surface temperature of the material rises, resulting in metamorphism, melting, ablation, evaporation, etc.
Cold Processing
Cold processing emits a photon with high load energy (UV), which can destroy material or chemical bonds in the surrounding media. As a result, the material suffers non-thermal process degradation. Because it is not a hot ablated process, cold work has a specific significance in the laser marking process.
Cold stripping has no thermal side effects and destroys the chemical bonds. Consequently, thermal deformation caused by heating and so on will not occur in the inner and outer sections of the surface. For example, an excimer laser deposits a chemical coating on a substrate in the electronics sector to make a narrow groove on the semiconductor substrate.
What is MOPA laser marking?
The Master Oscillator Power Amplifier, or MOPA, is a device that combines a master laser with an optical amplifier to increase output power. As a result, this fibre laser is one-of-a-kind and cutting-edge equipment that may help you achieve maximum efficiency in your business.
It is a flexible technique that may be suitable to measure pulse duration and mimic the features of ordinary fibre lasers. To improve dynamic oscillation characteristics, the marking machines use a modulated seed laser. MOPA lasers are well suited for applications needing high power output and a wide variety of pulse frequency ranges.
The MOPA laser system, on the other hand, provides improved control over peak power and pulse width by utilizing pulse tune functions that maintain high repetition rates at high power output. For modifying laser parameters, the MOPA fibre laser has many tuning options. This approach frequently results in high-quality colours and a powerful visual impact.
What is Laser Cutting?
Laser cutting uses a laser to cut, slice, engrave, or otherwise change physical materials. As modern as it may sound, laser cutting is a technique that has been around for decades. Its reach was first limited, as with many breakthroughs, but numerous industries have eagerly adopted it.
The automotive, castings, moulds, tools, jewelry, and medical sectors are the most prevalent uses for laser cutting. In addition, it is also suitable to make parts for medical equipment, computers, and electronics, among other things. Laser cutting is a fantastic choice for difficult or impossible materials to cut using conventional methods.
Fibre laser cutting process
Laser cutting directs a beam or material using a high-power laser directed by optics and computer numerical control (CNC). Consequently, a motion control system follows a CNC or G-code of the design to cut the material. The concentrated laser beam burns, melts, and vaporizes the materials to leave a high-quality surface completed edge.
According to the laser principle, activating lasing materials with electrical discharges or lamps inside a closed container produces the laser beam. The process then amplifies the lasing material internally through a partial mirror until its energy is sufficient to exit as a stream of coherent monochromatic light. Mirrors or fiber optics pass the beam via a lens that enhances it, focusing on the work area.
C02 vs. Fiber Laser: Which one should you choose?
Fiber lasers are ideal for high-contrast marking applications such as metal annealing, etching, and engraving. They have a small focus diameter and a high intensity, making them excellent for the permanent marking of serial numbers, barcodes, and data matrices on metals.
This laser intensity sometimes becomes 100 times greater than the CO2 laser source. Fiber lasers are popular for product traceability and identification, metal cutting, and engraving.
Non-metallic materials such as plastics, fabrics, glass, acrylic, wood, and even stone are appropriate for CO2 laser engraver. They designate PVC pipes, building materials, mobile communications devices, electrical appliances, integrated circuits, electronic components, and pharmaceutical and food packaging.
C02 Laser Engraver | Fiber Laser Engraver | |
Metal Engraving | Not suitable as Fiber Laser | Appropriate for metals |
Better For Cutting | Better | Relatively not suitable for all metals |
Engraving Time | Slow Cutting | Fast Cutting |
Maintenance Time | Need more maintenance | Low maintenance |
Lower Cost | Cheaper | Relatively Expensive |
Laser machines on the market
We’ve seen a significant change in the marketplace as machines become more economical. Laser engraving machines, formerly only used in industry, may now be found in schools, creative spaces, and even households.
This section will highlight the most common types of laser machines. We will not focus on the machines but on the types of laser sources these machines are using.
Fibre laser cutting machine
The Fibre Laser Cutting equipment is mighty and can cut through thick metals. Fibre-optic laser cutters cut metals at fast speeds and with greater accuracy. It is a technology that has been on the market for more than 20 years.
However, the fiber laser cutting machine uses a fiber laser source for cutting. These devices consume a lot of energy and require an oxygen cylinder to operate and function. For Example, These devices can cut metals ranging in thickness from 0.5mm to 20mm. Besides, these machines have sizes ranging from 1500mm x 2000mm to 2500mm x 3500mm.
Fibre laser engraver
The fiber laser engraver utilizes a similar power source as the fiber laser cutting machine, requiring less power. While a fiber cutting machine requires a minimum of 300W, a fiber marking machine requires a maximum of 120 to 150W.
For Example, the fiber laser cutting machines have power supplies ranging from 300W to 8000W. On the other hand, the power supply for fiber laser engraving machines is 5W to 120W. These power configurations are insufficient to cut metals at high speeds, like fiber cutting machines.
CO2 laser engraving machine
A CO2 laser engraver is the most accessible and cost-effective method of laser engraving. Usually, the machine’s base has a water-cooled glass tube, and machine bed sizes range from A4 to A3.
A CO2 laser engraver can often cut non-metals, engrave them, and provide excellent plastic, wood, and leather results. They also give good results on coated metals like anodized aluminum and powder-coated steel.
UV laser marking machine
UV lasers vary from their CO2 or fiber-based counterparts in that they do not harm the materials around the surface and use a far lower power type of marking.
It makes them the finest of the group for marking since they are excellent for everything from fruit to glass, Teflon, diamond, silicone, plastic, and precious metals. A UV laser may be suitable to mark nearly anything.
Solid state laser marking machine
A typical solid-state laser marking machine uses a crystal as an amplification medium. A laser diode or discharge lamp pumps the laser away in the process. Consequently, the most common crystals used in marking applications emit at roughly 1m and are Nd: YAG and Vanadate crystals.
The crystal medium produces a high concentration of atoms, resulting in light amplification. The peak power of these lasers can be rather considerable. However, because the crystal warms up quickly, the average power must be much lower than in other lasers. It implies that the pulses can have a high repetition rate for a brief time.
Diode Laser Machine
DDL, a direct Diode Laser machine, also famous as an injection laser or semiconductor pumped laser marking machine, combines light from many diodes into a single beam. It then directs it directly to the point of interest.
These diode lasers emit coherent light in the visible and infrared ranges. If one compares laser power to input power after removing the fiber system, these lasers are significantly more efficient.
However, the diode pump laser marker is appropriate for marking on electronic, PVC, auto parts, jewelry, metal and tool items, medical tools, switchgear industries, instrument marking precision applications, etc.
Summary
Above all, the required material quality and total cycle time all play a role in selecting the best laser engraving machine for your project.
Laser marking discolors the material’s surface, whereas laser etching and engraving remove a bit of the surface area as they mark. The primary distinction between laser etching and engraving is the depth the laser penetrates the surface.
Finally, here’s a quick breakdown of the differences between laser marking and laser engraving.
Laser Marking | Laser Engraving |
Modify material properties such as surface appearance. | Melting, vaporizing removes the material |
Does not damage the material’s outer surface | Removes the engraved materials from the surface |
Low laser beam power | High power laser beam |
No marking depth as it doesn’t remove any materials from the surface | Makes a specific engraving depth |